Industry 4.0
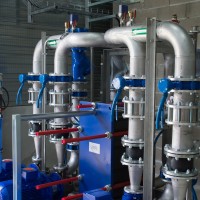
Industry 4.0, smart factories, the Industrial Internet of Things… whatever you choose to call it, it’s certain that manufacturing is changing in extremely significant ways right now.
We can’t resist those changes or ignore them. They’re coming whether we want them in our facilities or not. They will change work and the pace of progress for early adopters, and they will change the competitive landscape for those who try to stave them off. So staving them off won’t be a possibility for long.
But keeping up with them is something else entirely.
- The Internet of Things refers to the ability of machines to communicate with one another, as when a valve signals that it needs service before it breaks or a printer signals its need for more ink (or other raw materials) just in time for a refill.
- Open source and non-proprietary code is essential for communication among machines.
- More common machine languages are becoming an important part of the paradigm; machine builders, analysts, and engineers need to be able to communicate smoothly just as much as machines do.
- Additive manufacturing, or 3-D printing, is changing the face and the experience of prototyping.
- Integrated systems throughout and among facilities make big things possible.
- Big data, automated analytics, and friendly user interfaces allow data-driven decisions in real time.
- Always-on users, from machine operators using a kiosk to engineers using a tablet to workers in the field using phones — and back to the C-suite with desktops — are driving greater compatibility.
- Augmented reality allows closer communication at a distance.
In some cases, Industry 4.0 will lower the bar to entry and in some cases it will ask too much of companies with limited resources. In every case, it demands that we look ahead.
Knowledge is power.